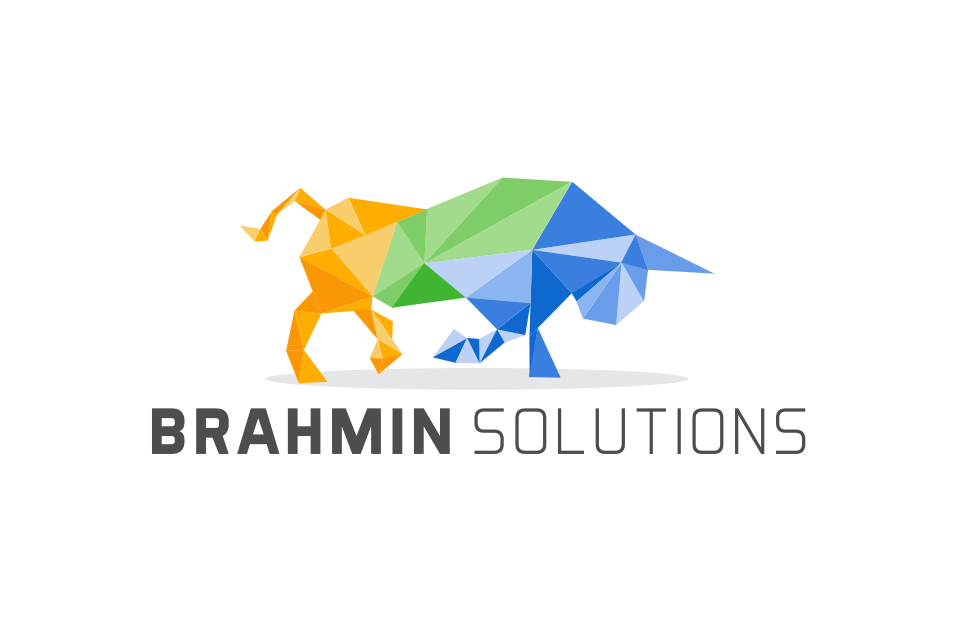
Manufacturing and Inventory Management Software
Hmm, mom's mac and cheese.
A dish all your close family begs your mom to make for thanksgiving. YUM!
A recipe only she can replicate, no matter how many times you have tried to make it, it never comes out the same.
Your mom's recipe is known as a bill of materials.
A bill of materials (BOM) is a recipe or a set of instructions to build a product. In your mom's case, that delicious mac and cheese. It will contain raw materials, assemblies, subassemblies, as well as quantities required to produce a product.
Just like the recipe for your mom's dish, all products will have a BOM that will tell you what goes in and how to make it.
It is meant to be followed to the letter and is a core element for any production management.
In this article, we'll explore manufacturing bill of materials, what it is, how to create one, and what tools you can use to help you along the way.
A bill of materials (BOM) is a list of raw materials, sub-assemblies, components, instructions, and quantities needed to manufacture a product.
A well-detailed bill of materials will include more instructions than just the list of items needed to create the finished product. It will consist of operations and product routing.
It may also include the time effort, equipment, and machinery required to build the product.
As you can probably imagine, the complexity of a BOM depends on the complexity of the product. A manufacturing BOM for a car might fill a binder while a BOM for a chair could fit on a napkin.
Bill of materials are meant to be followed very precisely and are an essential part of any manufacturing process.
Let's take a look at the types of BOMs and when your business would want to use them.
A bill of materials is a critical part of any company, but there are many types to choose from. This article will give you an overview of some different BOMs and help you decide which type would work for your business.
Manufacturing Bill of Materials (MBOM)
A manufacturing bill of materials displays the raw, and in some cases pre-processed resources needed to produce a finished good. These are broken down into assemblies and subassemblies that will be combined with other parts or pieces until they ultimately become one product.
Engineering Bill of Materials (MBOM)
An engineering bill of materials is meant to define the design for a finished product and differs from manufacturing BOMs in that it focuses more on specific designs rather than production. It is usually created using computer-aided design or CAD software such as Solidworks or, in the case of an electrical assembly, with electronic design automation (EDA).
An EBOM should include a list of parts, components, and materials with detailed engineering information such as specifications, tolerances, and standards.
Phantom Bill of Material AKA Modular BOM
BOMs that describe a subassembly are referred to as Phantom BOMs or Modular BOMs.
A subassembly is a unit that is assembled separately and then used in a larger manufactured product.
Let's take a look at your mom's famous mac and cheese example to understand subassembly better. If your mom makes the Elbow pasta needed for the mac and cheese in-house rather than buying it from the store, that would be a subassembly. She would need to make the dough and then the pasta before making her mac and cheese. That process is separate from the final production process.
To capture this process, you will need to use a phantom BOM to group components under one bill of material. Why? To make the maintenance of the BOM much simpler given that a BOM can be a very long and complicated process and when making slight changes, it can be made to the Phanton BOM without having to disrupt the complete BOM each time.
For example, if the dough changes, all you need to do is make an edit on the Phantom BOM rather than the final BOM.
Configurable BOM
A configurable bill of materials (CBOM) is used when a product has multiple variations.
For example, if you are selling a Bed with different sizes (Full, Queen, King or Cal King), colors (Black, White, or Brown), and frames (Box Spring, Divan Bases, or Adjustable Bases).
A CBOM is used to create products the company sells dynamically. The main goal of a Configurable BOM is to reduce the effort it takes to maintain the product structures. If you consider the bed example from above, it has 36 variations. It is easier for all the different options to be maintained in one BOM rather than 36 BOMs.
To create an effective CBOM, you must use a phantom BOM.
Phantom BOM will allow you to set up sub-assemblies that can be selected to configure an end item. Going back to our bed product, use Phantom BOMs for different types of frames and bed sizes. It makes it easier to maintain.
Multi-level BOM
A multi-level BOM is a nested list that includes components, parts, and assemblies needed to make the final product.
It displays all the items in a hierarchical view or parent-child relationship. When an item is a sub-component, all the components including the finished parts and raw materials are shown in the BOM.
Think of a multi-level BOM as a tree with several branches and leaves.
A single-level BOM contains only one level of children in assembly and only the components needed to make that assembly are listed.
As you can see, each product doesn't always fit a specific BOM type. Sometimes you need to use multiple BOMs to create an efficient structure.
BOMs should be designed in a way that fits your business. It should be flexible enough for changes and accurate enough to be followed by anyone.
That is the primary purpose of a BOM.
If you are a manufacturer, you must use a bill of materials, and using the BOM types mentioned above will help you organize your recipes.
But the benefits of using BOMs extend far beyond organizing of your finished products and raw materials. Here are some more advantages.
Buy organizing your materials, subcontracts, and subassemblies; You can easily see the cost of the product. Having visibility of your COGS for your finished product will help you maintain the best possible profit margin.
If you need to swap materials or parts to reduce your costs, you can use the BOM to quickly interchange parts and get a quick look at your new product cost.
By using BOMs, your manufacturing software can alert you when you are running low so that you can purchase enough to meet your demand.
This can help you have sufficient stock to produce your finished goods and make on-time deliveries to your customers. On-time delivery means happy customers. Happy customers mean they will reorder again and leave you positive reviews.
Learn more: Key Aspects of Inventory Control in Manufacturing Industry
Knowing what parts, how much of it you need, and the time it takes to put it all together, makes it easy for you to start estimating delivery times to your customers.
By knowing all the steps to create a finished product, you can make sure each step happens in time.
You can also make decisions to help speed up your delivery times. Let's assume your business manufactures bikes and most of your bikes have a sub-assembly for the part, tire. By having a structured BOM, you can see the benefit of making tires in a completely separate production rather than in each bike production. That means you are going to assemble finished tires every day (Make to Stock) so that your bike production process doesn't have to wait for tires to be sub-assembled every time. They can just go pick up the tires and assemble the bike.
This will allow you to save time, reduce labor costs, increase profits, and guarantee faster delivery times.
Another reason why BOMs are essential in manufacturing is to reduce waste.
Waste can come in many ways. One way is from your manufacturing process, and the other is having excess inventory.
With BOMs, you know the exact quantity you need to produce your finished product, including the ratios. This will make sure you are not using too much of one product, which could cause you to scrape the whole production and start over.
Ordering excess inventory because you don't know your production demand will lead to wastage. Inventory is cash and having cash tied up in unnecessary stock will slow down your business growth.
Now that you have seen the excellent benefits of using BOMs, let us show you how you can put them together.
We will walk you through a simple BOM and start adding options and subassemblies.
Let's assume you are a furniture manufacturer and produce chairs.
The first job you need to do is to list the items that go into making this chair along with the qty and cost.
Chair
Total Cost = $20
Perfect! Are we done?
Well not entirely, if your production process is simple where it's just a collection of raw materials and then assembly, then yes! If not, let's continue.
Most of the time, the production process is not as simple. Your chair could come in multiple colors and sizes. The backrest you are using might be assembled first. So let us look at how that example would look like:
Chair
Total Cost for Small Chair = $25
Total Cost for Large Chair = $27
Wow! That looks like a detailed BOM. We have used all the types discussed above.
Are we done now? No. What about operations that are needed to complete this BOM?
Let's add the operations and see what the final BOM would look like.
Chair
Materials
Operations
Painting .5 Hr @ 20 / Hr
Drying 2 Hrs @ $5 / Hr
Assembly .5 Hr @ $20 / Hr
Total Production Time: 3 Hrs
Materials Cost: $25 - $27
Operations Cost: $30
Total Cost for Small Chair = $55
Total Cost for Large Chair = $57
Now let's compare our original BOM to the configurable BOM. It looked like it only cost us $20 to build a chair, but the actual cost was almost triple that. Creating a detailed BOM will allow you to see the true cost of manufacturing, but you don't have to do it alone. You can use Manufacturing Software to make this process much more manageable.
We got through what bill of materials are, why they're essential, and how to make them.
But where do you keep them and update them?
Unlike your mom's recipe, which is probably memorized or on some piece of paper, a complex BOM must be on software. If you manufacture simple products like the first BOM we have created with no options, then you can use spreadsheets, but anything more, you must use a manufacturing software.
Think about managing subassemblies on spreadsheets? Your material prices will change over time, they will either go up or down, and your software can calculate this in real-time.
So is there a software that can help me automate my BOM creation and my production processes?
Well, you are in luck.
You can now use a Manufacturing Software, like Brahmin Solutions, to track your BOMs into your inventory and entire workflow.
That means you can track your production processes and sales from a single dashboard.
Brahmin Solutions doesn't just provide a manufacturing software. It provides a complete inventory software and warehouse management software that allows you to connect to eCommerce channels, shipping platforms, and sell wholesale by providing your B2B customers an order portal where they can place orders at their convenience.