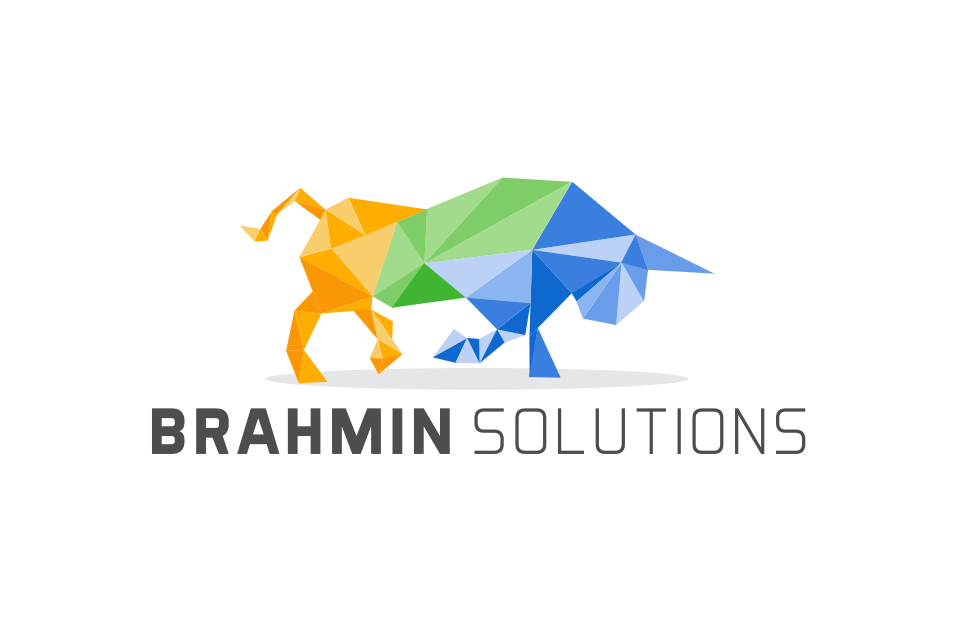
Manufacturing and Inventory Management Software
Have you ever wondered what it really costs to make your product? As a manufacturer, knowing the total cost of manufacturing isn't just a "nice-to-have" — it's something you absolutely need to know. When you take the time to figure out these costs accurately, you gain insights that can push your business forward, helping you make smarter decisions that will pay off in the long run.
Think of it like this: if you don’t fully understand your costs, it's like trying to find your way with an incomplete map. You might end up with gaps in your financial statements, unsure of where your money is really going. By knowing your manufacturing costs, you gain better visibility into your production processes, helping you spot opportunities to cut costs, streamline operations, and boost profitability.
Imagine realizing that a small tweak in the way you use raw materials could save you thousands each year. Or that outsourcing certain operations could cut costs significantly. These kinds of insights are only possible when you really understand your total manufacturing costs.
In this guide, we’ll break down exactly what goes into calculating these costs, why they matter, and how you can use this knowledge to become more efficient and profitable. Whether you're new to manufacturing or just looking to get a better handle on your expenses, this guide has got you covered. Let's dive in and uncover the secrets of your production costs!
Total manufacturing cost is the sum of all the expenses you incur to produce your finished product. It includes the cost of raw materials, direct labor, and manufacturing overhead. Understanding these components is the key to calculating your production costs accurately and getting a good grasp on how your business runs.
To break it down, total manufacturing cost has three main components:
Each of these components plays a crucial role in your overall cost structure, and by understanding them, you can better manage your production budget and make smart decisions to improve efficiency and profitability.
To truly understand your total manufacturing costs, let's dive deeper into each component and see what makes them so important.
Direct materials are all the physical items that go into making your product. This could be anything from raw materials like wood for furniture, to parts and components like screws or bolts. It also includes any packaging materials that are essential to your finished product.
Think about it like this: if you're making a wooden chair, the wood, screws, and even the varnish are all considered direct materials. These are the materials you can easily trace to the final product.
How to Calculate Direct Materials Cost:
To calculate the direct materials cost, use the formula:
Direct Materials Cost = Beginning Inventory + Purchases During the Period - Ending Inventory
Example Calculation:
Let's say you start the month with $10,000 worth of wood in inventory. During the month, you place a purchase order for an additional $5,000 worth of wood. By the end of the month, you have $3,000 worth of wood remaining.
Direct Materials Cost = $10,000 (Beginning Inventory) + $5,000 (Purchases) - $3,000 (Ending Inventory) = $12,000
This means you spent $12,000 on materials during the month.
Direct labor refers to the wages paid to the workers who are hands-on in creating your product. These are the folks who assemble the parts, operate machinery, or perform tasks that directly add value to the finished product.
But direct labor costs go beyond just wages. They also include payroll taxes, insurance, and other employee benefits. Essentially, anything that adds to the cost of employing the people who make your product counts as direct labor.
How to Calculate Direct Labor Cost:
To calculate direct labor cost, use the formula:
Direct Labor Cost = Total Labor Wages + Payroll Taxes + Benefits
Example Calculation:
Imagine you have three workers who are each paid $20 per hour. Each worker worked 160 hours in the month. In addition, payroll taxes and benefits add an additional $5 per hour per worker.
Total Wages = 3 Workers × $20/hour × 160 hours = $9,600Payroll Taxes and Benefits = 3 Workers × $5/hour × 160 hours = $2,400
Direct Labor Cost = $9,600 + $2,400 = $12,000
So, the total direct labor cost for the month is $12,000.
Manufacturing overhead includes all the indirect costs that are still necessary for production. This could be things like electricity to run the machines, rent for the factory, or maintenance costs for the equipment. While these costs don’t directly touch the product, they’re crucial for keeping your operations running.
A good way to think about it is: if you turned off the power, could you still make your product? If the answer is no, then those power costs are part of your manufacturing overhead.
How to Allocate Manufacturing Overhead:
Overhead costs are often allocated based on a predetermined rate. One common way to do this is by using a percentage of direct labor costs or machine hours.
Example Calculation:
Suppose your total overhead costs for the month are $15,000, and you produced 1,000 units. The overhead cost per unit would be:
Overhead Cost Per Unit = Total Overhead Costs / Total Units Produced
Overhead Cost Per Unit = $15,000 / 1,000 Units = $15 per unit
Understanding these components in detail helps you see exactly where your money is going. It gives you a clearer picture of your expenses, and from there, you can make better decisions to cut costs, improve processes, and ultimately boost profitability.
When managing your production costs, it's important to understand the difference between direct and indirect costs. Direct costs are easy to trace directly to the production of your product, while indirect costs are necessary but not directly tied to each unit you produce.
Direct Manufacturing Costs are the raw materials and labor used to create your product. These are the costs that you can see and measure easily — things like the wood for a chair or the wages paid to the person assembling that chair. If the cost contributes directly to making the product, it’s a direct cost.
Indirect Manufacturing Costs are the expenses that support the production process but aren’t directly tied to a specific product. These include things like the electricity to power the machines or the rent for the building where production takes place. They are crucial for keeping everything running but aren’t part of the product itself.
Understanding the difference between these two types of costs can help you avoid double-counting expenses and ensure you are accurately calculating the true cost of manufacturing your products.
Brahmin Solutions makes calculating manufacturing costs easy by automating the entire process. Instead of manually tracking expenses and crunching numbers, you can use Brahmin Solutions' MRP software to keep all your costs in one place. Here’s how Brahmin Solutions simplifies the calculation of each cost component:
Direct Materials Calculation
Brahmin Solutions tracks your raw materials in real-time, including inventory levels, purchase orders, and usage. With all this information readily available, the system can automatically calculate your Direct Materials Cost using the formula:
Direct Materials Cost = Beginning Inventory + Purchases During the Period - Ending Inventory.
For example, if you start the month with $10,000 worth of steel, buy another $5,000 worth, and end the month with $3,000 left, Brahmin Solutions will automatically calculate your direct materials cost as $12,000, saving you time and reducing human error.
Direct Labor Calculation
Brahmin Solutions can also track labor hours and costs. By inputting employee wages, working hours, and other related costs such as payroll taxes, the system can calculate your Direct Labor Cost seamlessly.
For example, if three employees work 160 hours each at $20 per hour, with additional payroll costs of $5 per hour, Brahmin Solutions will automatically calculate the direct labor cost as $12,000.
Manufacturing Overhead Calculation
Manufacturing overhead costs are often the most challenging to track manually. Brahmin Solutions helps by centralizing all indirect costs such as utilities, rent, and maintenance costs. The software allocates these costs based on your preferred method (e.g., machine hours or labor hours).
If your monthly overhead costs are $15,000 and you produce 1,000 units, Brahmin Solutions will calculate the Overhead Cost Per Unit as $15, giving you a clear understanding of your overhead allocation.
Total Manufacturing Cost Summary
With Brahmin Solutions, you can see all your costs—direct materials, direct labor, and overhead—combined in one simple summary. For example, if your direct materials cost is $12,000, direct labor is $12,000, and overhead is $15,000, the Total Manufacturing Cost is:
Total Manufacturing Cost = Direct Materials + Direct Labor + Manufacturing Overhead
Total Manufacturing Cost = $12,000 + $12,000 + $15,000 = $39,000
Brahmin Solutions provides you with a real-time view of your costs, helping you make adjustments on the fly and keep your production as efficient as possible.
Cost Reports and Insights
In addition to calculating costs, Brahmin Solutions provides detailed cost reports, allowing you to track cost trends over time. With this visibility, you can identify inefficiencies, make data-driven decisions, and set pricing strategies that ensure profitability.
By using Brahmin Solutions, you can automate the process of calculating and tracking your manufacturing costs, saving time, reducing errors, and ultimately boosting your bottom line.
Reducing manufacturing costs is key to increasing your profit margins. Here are some strategies to help you cut costs without compromising quality:
By taking proactive steps to manage and reduce your manufacturing costs, you can improve your bottom line and make your business more competitive in the market.
It’s easy to confuse total manufacturing cost with the cost of goods sold (COGS), but they are different concepts. Total Manufacturing Cost refers to all the costs involved in creating your product, including materials, labor, and overhead. COGS, on the other hand, is the cost of the inventory that was actually sold during a specific period.
Think of it like this: total manufacturing cost is about what it costs to make the product, while COGS is about the cost of the product that you’ve sold. Knowing both figures is important for understanding your profit margins and financial health.
Calculating your total manufacturing cost isn’t just about understanding your expenses — it’s also a powerful tool for improving productivity. By knowing exactly what each part of your production process costs, you can:
Keeping track of your actual total costs against your estimated costs helps you stay on top of your business finances. This can help you see if you’re underestimating or overestimating your production costs, allowing you to make better decisions moving forward.
Understanding your total manufacturing costs is a game-changer for any manufacturer. It gives you the insight you need to make informed decisions, optimize your production processes, and ultimately boost your bottom line. Whether it’s cutting down on material waste, negotiating better deals with suppliers, or streamlining labor efficiency, knowing your costs is the first step to greater profitability.
If you want to simplify the process of tracking your costs and improve visibility into your production, consider using an MRP system like Brahmin Solutions. With the right tools in place, you can take control of your manufacturing costs, make better business decisions, and grow your profitability.
Ready to learn more? Book a demo with one of our product consultants today and see how we can help you transform your manufacturing operations.