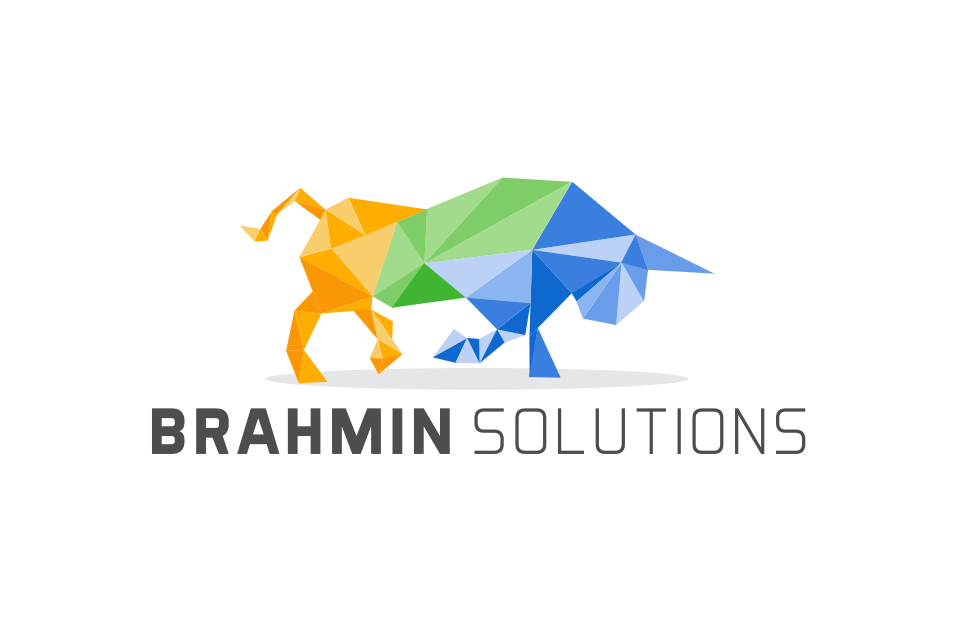
Manufacturing and Inventory Management Software
There are many different types of inventory management. Every business is different, so it is important to find the best type of inventory management for your company. You can learn about different techniques to make the best decision for your company.
This guide outlines the types of inventory with real-world examples.
Raw materials are the materials used to create finished products. They can be items produced by your business or purchased directly from vendors. When the product is completed, the raw materials are different than their original form. For example, oils that go into making a bar of soap.
They are similar to raw materials in that a business uses materials to create and finish products, except they remain recognizable when a product is completed, such as a screw or a tire that goes into a car.
Work in progress (WIP) refers to unfinished items in the production process, sometimes called bulk products / intermediate products. In terms of a soap manufacturer, the work-in-progress inventory might be the soap that is drying and unpackaged and yet to be cut up into individual pieces.
MRO is inventory - often in the form of supplies - used to support and facilitate the production of finished goods. These items are consumed in production but aren't directly part of the finished product. For example, disposable molds used to manufacture soaps would be considered an MRO inventory.
Finished products are products that are sellable after the production process. In our example, this would be the soaps themselves packaged.
You will see many other terms such as “Transit Inventory”, Decoupling Inventory, Excess Inventory, and more, but these terms are used to describe the status and purpose of the inventory. The physical stock almost always falls into one of the five abovementioned categories.
Inventory tracking software, MRP systems, and ERP systems always track the first four types of inventories. However, good MRP/ERP software may also allow you to track maintenance, repair, and operations inventories (MRO) such as nuts, bolts, belts, tape, glue, or other materials used to maintain the factory and assist in operational operations functions.
There are different ways to track different types of inventory, and it largely depends on the inventory management system you use. Each technique has its own goals that match the industry, company size, or finished product structure. These techniques include:
Economic order quantity is a formula businesses use to determine the best time to reorder inventory to minimize both ordering costs and holding costs. This method is often used by process manufacturing companies that produce products in bulk. These companies can purchase materials in bulk because they know precisely how many products they will be able to produce. They can include variables like demand rate, inventory holding cost, and others to figure out when they should make a large purchase in order to reduce the number of times they have to buy supplies. Producing products in volume helps them hold down costs, which improves their cash flow.
The minimum order quantity (MOQ) is the smallest number of products a manufacturer will agree to sell. This usually means you need to order at least a dozen or a hundred, depending on the product. Having a MOQ in place allows manufacturers to produce products more efficiently, enabling them to track inventory more accurately.
A just-in-time (JIT) inventory system is designed to minimize inventory storage costs by keeping only the minimum amount of items necessary on hand. For a JIT system to work, you need a good understanding of the manufacturing process and robust supply chain management skills.
ABC analysis is a way to rank finished goods by how profitable they are. A is the most profitable, then B, and finally C which is small or has low margins. The goal of inventory management is to have enough material for high-level production. The urgency for other categories decreases accordingly. If there is a disruption and insufficient material, then sacrifices can be made on the lower tiers to ensure the most profitable finished goods are still made.
The inventory control technique you use will affect the type of inventory tracking you need. Each of the above methods also introduces limitations to manual inventory tracking. For example, ABC analysis can be highly subjective when done by hand. MOQ and Economic Order Quantity formulas can be inaccurate or produce errors. SMEs can use affordable inventory or MRP software to manage any of these inventory techniques effectively and without human bias or error.
Several tools can be used to help automate the inventory management process. These tools can be connected to the inventory software or MRP software so that the entire process is automated. This will help keep the inventory process running smoothly and near real-time. Some examples of tracking tools are:
Barcodes and QR-codes are common today. They are used on items like raw materials. People can use scanners to read the codes. This is helpful because it allows people to track materials throughout the production process. This information can then be used to update records in an MRP system.
RFID is another way to identify materials. It uses chips that send a signal to Wi-Fi or scanners to say where the material is. Active RFID uses a chip that sends a signal. Passive RFIDs do not have a chip that sends a signal but can be read by hand or embedded scanners.
Some machine manufacturers include a way to measure how much material is used to produce a product. This can be done by connecting the machine to inventory tracking software. Or, the values can be added manually as reports are generated and added manually at an operator station or through administrative means.
Small and medium-sized businesses (SMEs) must deal with unreliable or unpredictable supply chains. This can be because they are smaller companies, and manual inventory tracking can cause errors, human bias, and inadequate stock-level decision-making analysis. However, today's traceability software platforms (such as MRP and ERP) are agile, flexible, and designed even for SMEs. This allows these smaller companies to utilize best-in-class software comparable in functionality to platforms used by large companies.
SMEs can use software to help track inventory. This will ensure that they always have the materials they need and are in the right place at the right time.
Stock Keeping Units - also known as SKUs - are item codes that you and others use to search and identify items.
Make sure to add an SKU to each inventory type mentioned above if you use it for your business. Setting up an easy-to-understand system for SKUs is vital because this will allow you to identify, differentiate and monitor your inventory.
Stick to an alphanumeric system for your SKUs and avoid accents and symbols that can cause issues when using spreadsheets. It’s easier to start with an SKU numbering convention as early as possible because it gets more challenging when you have many items.