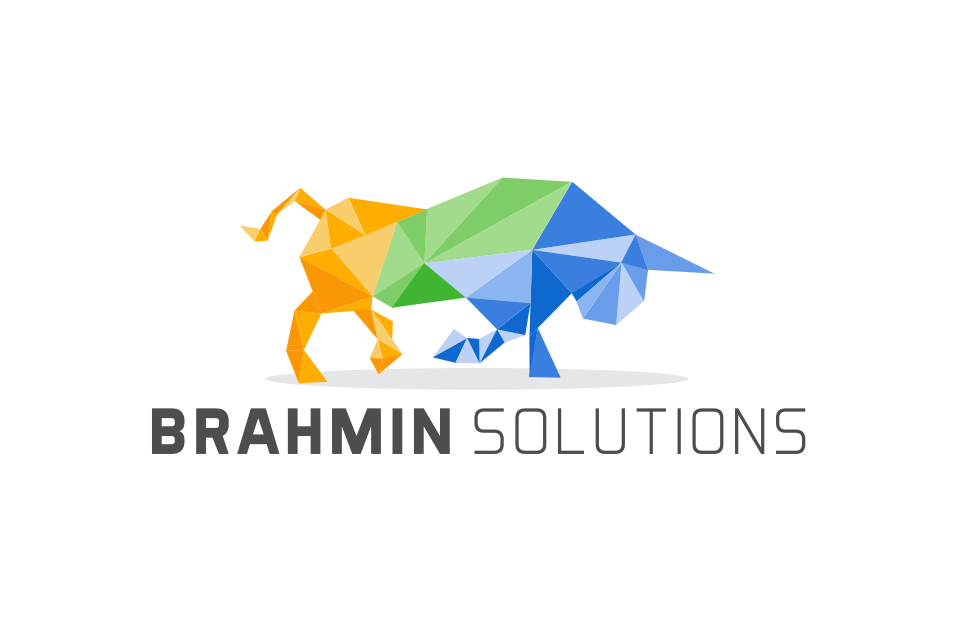
Manufacturing and Inventory Management Software
What images dance in your head when you hear the term 'manufacturing processes'? Do visions of infinite assembly lines and gargantuan machinery take center stage?
That depiction might have hit the bullseye back in the early 1900s. Yet, today, the manufacturing landscape is a kaleidoscope of diversity. A myriad of manufacturing types now exist, some of which might even catch you off guard. It's safe to say the industry has come a long way since the industrial revolution.
Take a peek at the varied facets of the manufacturing industry:
These six sub-sectors, each a cog in the vast manufacturing machine, employ distinct processes to churn out their products. In this article, we're going to plunge into the six types of manufacturing processes. But first, let's demystify the concept of the 'manufacturing process' before we navigate through its diverse types.
Manufacturing is an intricate dance of sequential steps, blending together the expertise of individuals and the power of machinery to transform raw materials into a finished product. These processes can seem daunting, even to experienced engineers. That's why we've decided to create this easy-to-understand guide, breaking down the six unique types of manufacturing processes for you.
Within the expansive manufacturing industry, several key sub-sectors exist, including food, textile, electronics, wood, and chemical manufacturing. Each of these sectors utilizes a distinct set of processes and steps to create the end product. The selection of the appropriate manufacturing process is influenced by a myriad of factors, such as consumer demand, technical capabilities, available resources, and the required turnaround time. As with anything, each manufacturing process presents its own set of benefits and drawbacks. Manufacturers carefully weigh these factors in deciding the most suitable approach for their business.
When it comes to the manufacturing process and choosing the right one for your products, it’s often a battle between quality versus quantity.
Imagine a factory working round-the-clock, producing one product after another in a seamless, rhythmic flow. That's the essence of repetitive manufacturing, a traditional process deeply ingrained in our industrial landscape. Picture it as a tireless machine, humming along 24/7 to meet the ever-present consumer demand. This tireless rhythm can be sped up or slowed down as needed, giving manufacturers incredible control.
Repetitive manufacturing is a common sight in the automotive industry, where mass production is the name of the game. Its key strength lies in cost efficiency - it's a real money saver when it comes to producing components or products. Plus, it simplifies scheduling and offers clear performance visibility that can be closely tracked. It's a reliable workhorse of a process, and a staple in many industries.
Imagine a process that takes individual parts, components, and sub-assemblies and brings them together to create a finished product. That's discrete manufacturing for you! Just like its cousin, repetitive manufacturing, it utilizes assembly or production lines with a variety of setups and changeover frequencies. But the beauty of discrete manufacturing lies in its ability to create unique, standalone units. Picture the intricate craftsmanship of artisan furniture, the complex assembly of a smartphone, or even the monumental task of building an airplane. These are all feats of discrete manufacturing
Imagine a manufacturing process that thrives on creating unique, one-off products instead of mass production. This is exactly what the job shop manufacturing process does, stepping away from the usual dependency on assembly lines. It's a process that embraces limited automation, focusing instead on smaller, customized batches. The end goal? To replenish stocks once they're depleted.
What makes the job shop manufacturing process stand out is its adaptability. It's a system that welcomes change and makes effective use of resources. What's more, it gives you the flexibility to prioritize certain operations over others. A perfect example of this would be businesses that sell custom products like eyeglasses or stock frames. They are amongst the many enterprises that benefit from the unique advantages of job shop manufacturing.
Imagine a manufacturing process that churns out identical products, one after the other, without a pause. Sounds impossible? Well, it's not. Welcome to the world of process manufacturing, also known as continuous manufacturing. It's like the Energizer bunny of manufacturing, it just keeps going and going! Now, you might be thinking, this sounds a lot like repetitive manufacturing. And you'd be right! Just like repetitive manufacturing, process manufacturing operates 24/7. But here's where it gets interesting. This method of manufacturing doesn't just offer constant production. Oh no, it's got a lot more in its bag of tricks! It's like a well-oiled machine, offering businesses reduced manufacturing costs
Let's dive into the fifth type of manufacturing process - batch manufacturing, also known as process manufacturing. Think of it as a close cousin to discrete and job shop processes. The main idea here is to cater to larger consumer requirements, treating each one as a unique 'batch'. Once a batch is produced, the equipment undergoes thorough cleaning and preparation, gearing up for the next round of production.
There's a lot to love about batch manufacturing. For starters, it's cost-efficient, particularly when producing a whole batch of products at once. It makes the most out of resources, offers flexibility, minimizes waste, and keeps running costs low. Sounds pretty good, right?
But, like everything else, it's not without its challenges. You'll need to consider increased storage costs and put a rigorous quality control and assurance system in place. A batch gone wrong can mean higher costs and wasted time, which nobody wants.
Still, batch manufacturing proves its worth in various industries. From whipping up your favorite fast food meal and creating snazzy clothing to manufacturing electrical goods, pharmaceuticals, and even flatpack furniture, this process is quite the all-rounder.
Imagine a world, where a machine can create any object you desire, layer by layer, right before your eyes. Welcome to the thrilling realm of 3D printing, a manufacturing revolution that’s taking the globe by storm! Many industry insiders now acknowledge 3D printing as the sixth major manufacturing process, with its applications reaching far and wide.
Emerging from the innovative 1980s, 3D printing involves the creation of products using a variety of composites and materials, such as plastics and metals. The magic happens without the need for manual labor or automation. You'll be amazed to know that many businesses have already launched a diverse range of 3D-printed products into the market. From fashionable clothing to tantalizing food items, the possibilities seem limitless!
Are you thinking 3D printing sounds really expensive? You're not wrong. Between the time spent designing and developing the product, not to mention high-capacity printers that can cost anywhere from $50k to a whopping $500k, it can seem like a steep investment.
But here's a silver lining: the price of 3D printing technology is on a downward trend. As the Federation of American Scientists reports, “the price of 3D printing technology has fallen by about 80% over recent years.” So, while the costs might seem daunting right now, it's only a matter of time before they become significantly more affordable.
But the benefits of 3D printing extend beyond just cost savings. It also provides an opportunity to decrease financial capital, minimize waste, and conserve raw materials. Plus, it allows companies to create and test products before they decide to mass produce them. This innovative manufacturing process is already being implemented in the production of products such as:
No matter what manufacturing process your business might undertake, customers are only worried about the quality of the final product. Hence, in today’s competitive environment, it’s imperative to give utmost priority to the quality of the products and their assurance methods. As a business, choose the right process that fits your customer needs and use the latest technology to stay a step ahead of your competitors. With Brahmin Solutions MRP, you can closely watch the manufacturing process. From the bill of materials to production planning features, the solution helps you stay on top of your game and maintain the competitive edge for your business. Besides that, Brahmin Solutions also has important features like made-to-order and made-to-stock functionalities. This is your platform to scale up your business for better returns and bring efficiencies to the overall manufacturing process.