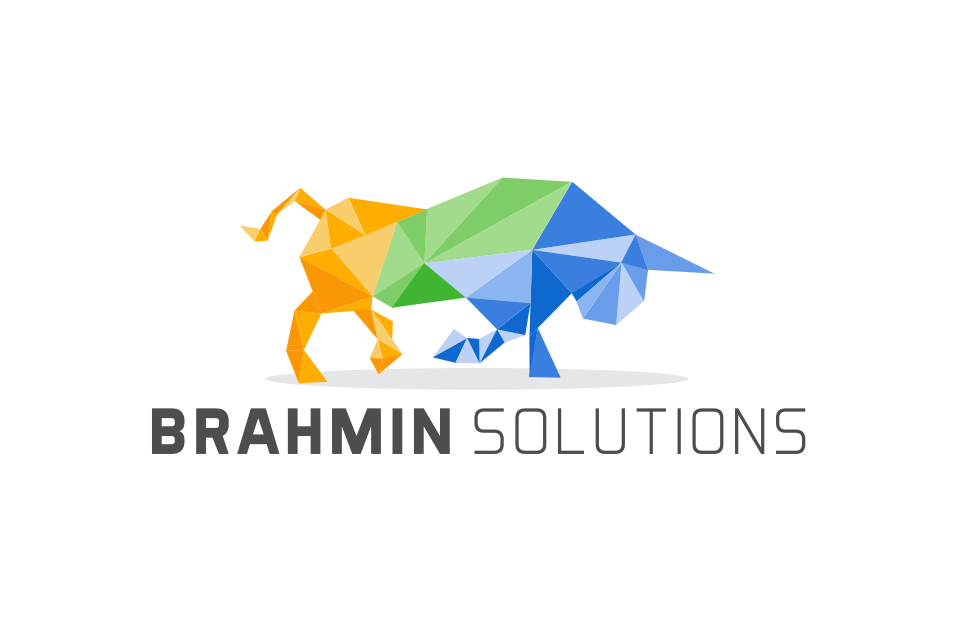
Manufacturing and Inventory Management Software
One of the major challenges for manufacturers, especially smaller manufacturers, is balancing supply with demand. It’s a delicate process, and if not executed properly, it can result in serious losses and challenges.
That’s where an MRP supply chain system can help. In this post, we’re going to cover the pros and cons of MRP systems so that you can better understand how it fits into your overall strategy and invest wisely.
Short for Material Requirements Planning, an MRP supply chain system matches your supply of raw materials with demands.
For instance, say your company sells candles. Every candle requires 10oz of wax and 10oz of glass.
Now, you may know that you need 200 candles stocked for the next month of sales based on your demand. However, that figure alone doesn’t provide a holistic view of what you need to order to meet the upcoming demand.
An MRP system fills in this gap. It uses software to automatically determine which materials you need based on demand. The software then automatically communicates this information to every department that needs it, keeping all of your teams and suppliers in sync.
Further Reading: The ultimate guide to raw material inventory management
An MRP supply chain system can be a massive help. It can also present unexpected challenges. We’ve listed the various pros and cons below so that you can better maximize the benefits of an MRP system while accounting for potential drawbacks.
As you might’ve guessed, one of the key benefits of an MRP supply chain system is that it makes it far easier to maintain communication throughout your departments. That’s because the system automatically keeps all dependent parties up to speed whenever your material needs change.
This happens whenever customer orders come in, trends are detected, and other changes in demand hit your database. As soon as these occur, the MRP system starts updating you and all involved parties so that you can buy more (or less) materials.
Two things that manufacturers are constantly working to avoid are stockouts and overstocking. Both can result in significant losses, but dodging them can require foresight you don’t always have.
With an MRP supply chain system, you can better your chances of correctly balancing your material planning. The system links up with your inventory data and demand predictors, allowing it to quickly find the ideal thread between the two.
Another pro to using an MRP supply chain system is that it makes it far easier to trace your supply chain. In industries where regulations play a pivotal factor (automotive, food, healthcare, etc.), this can be a critical feature of MRP systems.
For other industries, supply chain traceability can still be very useful. In both cases, it makes it easier to determine where issues are stemming from, reduce inconsistencies within your products, and solve various problems with your supply chain.
Financial losses aren’t the only consequence of stockouts and overstocking. They can also lead to inefficient uses of your resources. They require additional labor, time, transportation, and materials. Even if you’re big enough to absorb the financial cost, eating up resources can hit harder than you might expect.
If you’re running a tight ship, you don’t want to make these slip-ups. An MRP system can help you optimize your material planning, and by extension, your resources using calculations and automation.
This next benefit is more so a feature of automation than a specific feature of MRP systems. Every company can benefit from a reduction of clerical tasks. Much of the work involved with balancing your material planning involves repetitive bookkeeping.
An MRP supply chain system is excellent at handling this for you. In addition to making your workflows faster, this can reduce errors and free up staff (or yourself) to work on more high-value work.
When a customer places an order for your product, the top concern for that client is how quickly they will receive it. It’s up to you to provide them with an accurate (and hopefully prompt) timeline.
The problem is, calculating that timeline can be a serious challenge. Several factors go into predicting a delivery date. Fortunately, MRP systems can help. The software supporting MRP solutions not only optimizes your supply chain (allowing you to make more predictable timelines) but can also calculate these timelines for you. And if a delivery is going to be late, you can configure your MRP to automatically inform your customers, reducing headaches for all involved parties.
Finally, you can use MRP supply chain systems to scale your business more efficiently. Scaling up is usually a high priority for all businesses, but it comes with several challenges.
An MRP system makes this easier by automating segments of your workflow, cutting down on errors, and optimizing your material planning. By handling these tasks for you, you can scale up more confidently and dedicate more of your time to hit your goal of scaling up.
As mentioned, an MRP system isn’t without its challenges. One of the core challenges involved in implementing this kind of system is investing the initial resources to kick things off.
Predictably, the resources you’re going to need are time and money. You’ll most likely need to divert these from other aspects of your business, which is something you need to consider before investing in an MRP system. There will undoubtedly be a return on your investment, but whether or not you can afford to chase that ROI depends on your current capacity and resources.
MRP supply chain systems are not monolithic. There are various options available, each with its strengths, weaknesses, and feature sets. If you don’t know what you’re looking for, you probably won’t find it.
It’s best to meet with stakeholders and discuss the pros and cons of investing in an MRP system for your operation. Work together to list out your needs so that when it comes time to decide on an MRP, you can ensure that it’s a solution that aligns with your needs.
Having a conversation with your stakeholders is also a great time to check that everyone is on board. Anytime you’re investing in new software that everyone on your team is going to be using, this is something you’ll have to bear in mind.
Getting everyone on board not only means getting everyone excited (rather than frustrated by the change) but also providing training and an adjustment period.
Finally, an MRP supply chain system is only as good as the data you feed it. If you aren’t providing it with accurate data, you’re going to get inaccurate results.
Not only that, but because it’s an automated, integrated system, those inaccurate results are going to propagate throughout the rest of your software systems. So make sure ahead of time that your data is accurate, high-quality, and reliable.
Ultimately, the decision to invest in an MRP supply chain system comes down to your business’s unique needs and opportunities. Evaluate your needs, speak with stakeholders and team members to round out your perspective, and remember that you don’t have to invest in an MRP system today.
You can reach out to us at Brahmin Solutions today for expert insights and advice into whether MRP is right for your business.