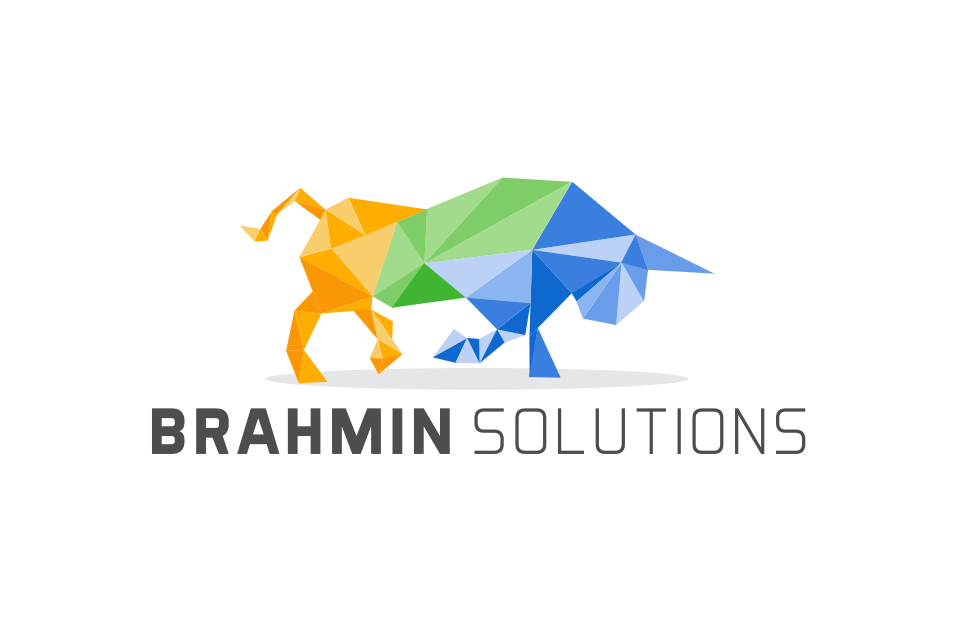
Manufacturing and Inventory Management Software
Lean manufacturing goes by many names: “Just-In-Time (JIT),” “The Toyota Way,” “The Ohno System” (after Taiichi Ohno, who was instrumental in its development within Toyota), and “quick-response manufacturing.”
It’s a technique used across the world by countless major brands to address the needs of their customers. So, let’s look at how lean manufacturing works and how you can use it in your business.
What started as a way to produce goods to meet exact customer needs, such as timeframes, quality, and quantity, has turned into a complete methodology that helps businesses create products with minimal waste.
Lean manufacturing applies Lean practices, principles, and tools to the development and manufacturing of products. Businesses that use lean manufacturing can benefit from a reduction in waste, better-optimized processes, lower costs, reduced time to market, increased innovation, and much more.
Adopting lean manufacturing can be tough, just like any change to how we work. Despite this, there are significant benefits for the businesses that can make it work. Here are just a few of the benefits you can expect when adopting lean manufacturing.
Adopting lean manufacturing can be challenging, but the benefits are worth it. Here are some of the advantages you can expect:
One of the biggest expenses in manufacturing is warehouse space. Every product and the materials needed to make them require space. Lean manufacturing reduces costs by ensuring you only stock the resources you need and hold minimal products in the warehouse.
By only keeping what’s necessary, lean manufacturing helps reduce dead stock. Dead stock is inventory that hasn’t sold and is just taking up space. Lean manufacturing can help eliminate this problem.
Lean manufacturing helps you get a better return on each product. With less waste and reduced warehouse costs, products can be shipped quickly, lowering the risk of extra costs related to holding inventory.
By adopting lean manufacturing, businesses can operate more efficiently and save money, all while meeting customer needs more effectively.
Lean manufacturing began in early 20th century Japan, specifically at the Toyota Motor Corporation. Originally a textile company, Toyota struggled with massive resource wastage when they moved into the automotive sector.
Shigeo Shingo and Taiichi Ohno, influenced by Frederick Winslow Taylor’s 1911 book, "The Principles of Scientific Management," worked with Toyota’s “Kaizen” improvement teams to create what we now call “The Toyota Way.” This method was also influenced by Japan’s poor economic situation after World War II. Ohno, after visiting supermarkets in the US, realized that work scheduling should be based on actual sales rather than production targets. This helped businesses produce only what customers needed.
Over time, companies worldwide adopted and modified this system. In 1988, John Krafcik rebranded it as "lean manufacturing" in his article “Triumph of the Lean Production System.” Krafcik stated that lean manufacturing plants have higher productivity and quality and that risks can be reduced by "developing a well-trained, flexible workforce, creating product designs that are easy to build with high quality, and having a supportive, high-performance supplier network."
From there, lean manufacturing continued to evolve into the system we know today.
The Toyota Production System (TPS) revolutionized automotive manufacturing by focusing on eliminating waste and optimizing efficiency. After World War II, Toyota faced significant financial constraints. This challenge led to the creation of TPS, which became synonymous with lean manufacturing.
At the heart of TPS are key principles that have driven Toyota's global success:
As with any methodology, lean manufacturing is centered around a clear set of principles. By following these principles, businesses can easily reap the benefits of lean manufacturing.
The first principle of lean manufacturing also doubles as the first step in your journey into becoming a lean business. The business needs to identify what its customers value and how its products can satisfy those values.
In the case of manufacturing, these values require businesses to:
By doing this, companies can create products that are tailored for their customers while reducing waste.
A value stream is the complete life cycle of a product. This includes the product’s design, the customers’ use of the product, and the disposal of the product.
By mapping out the value stream, it offers teams a clear visualization of the product’s life cycle that will make it easier to find and minimize steps that do not add value.
Product flow is crucial when it comes to lean manufacturing. An efficient product flow requires items to move from production to shipping without interruption. This is achieved by strategically organizing the work floor. A well-organized work floor results in reduced production time, inventory size, and material handling.
During this third step, it’s important to take into account every factor, from people and equipment to materials and shipping, to ensure products seamlessly move through the production process.
Traditional production systems utilize a “push” system (also known as “just-in-case” manufacturing), which involves pushing resources through the manufacturing process, even when there isn't an order. While push systems are easy to create, they often result in large inventories and a significant amount of waste.
A pull system is a far more lean-friendly production method that only gets to work when a customer makes an order. This allows businesses to only order resources as and when they need them and reduces the amount of stock sitting in a warehouse at any one time.
Using a pull system offers businesses additional benefits, including:
Moreover, the pull system helps in enhancing workflow efficiency. By streamlining processes and ensuring that every step in the production line is synchronized with demand, companies can significantly cut down on idle times and bottlenecks. For example, Hewlett-Packard implemented this strategy to deliver products just in time, thereby reducing expenses tied to surplus production.
However, it's essential to note some challenges associated with the pull system. While it brings many benefits, it requires meticulous planning and synchronization across the entire supply chain to prevent disruptions. Additionally, businesses might need to invest in inventory management software and training to ensure smooth adaptation to this system.
Adopting a pull-based production system involves a shift in mindset from traditional push methods, emphasizing responsiveness and flexibility. When successfully implemented, it allows businesses to remain agile, responsive to market changes, and highly efficient in their operations.
The final lean manufacturing principle is one that all businesses are working towards, regardless their methodologies. As you might expect, seeking perfection is often one of the most difficult principles to successfully apply in the workplace, as it requires continuous improvement and a shift in culture on an organizational level.
Lean manufacturing as a practice is a simple and . However, with the variety of industries availabe there are multiple ways to implement lean manufacturing. Here are a few techniques that you can implement with examples related to a specific industry:
Technique: 5S Methodology (Sort, Set in order, Shine, Standardize, Sustain)
Example: A dairy processing plant implements the 5S methodology to organize their workspace. They sort and label equipment and ingredients, arrange tools and materials efficiently, and standardize cleaning procedures. This reduces the time spent searching for items and ensures a clean, orderly environment, leading to increased productivity and hygiene.
Technique: Just-in-Time (JIT)
Example: An automotive manufacturer adopts JIT to align production schedules with customer demand. They receive car parts and components from suppliers only when needed, minimizing inventory costs and reducing waste. This streamlined supply chain allows them to respond quickly to changes in customer orders and market demand.
Technique: Six Sigma
Example: An electronics company applies Six Sigma DMAIC (Define, Measure, Analyze, Improve, Control) methodology to reduce defects in the production of circuit boards. By analyzing production data and identifying the root causes of defects, they implement improvements that enhance product quality and reduce rework costs, leading to higher customer satisfaction.
Technique: Total Quality Management (TQM)
Example: A pharmaceutical manufacturer embraces TQM by involving all employees in quality control and continuous improvement initiatives. They establish cross-functional teams to address quality issues and use customer feedback to refine their processes. This approach ensures consistent compliance with regulatory standards and high product quality.
Technique: Value Stream Mapping (VSM)
Example: An aerospace company uses VSM to map the entire production process of aircraft components, from raw materials to final assembly. They identify bottlenecks and non-value-added activities, such as excessive wait times between machining steps. By streamlining these processes, they reduce lead times and improve overall production efficiency.
These examples show how lean manufacturing techniques can enhance efficiency, reduce waste, and improve quality across various industries.
You don’t need to go it alone! Get in touch with us today, and let the experts at Brahmin Solutions help you get started on your lean manufacturing journey.