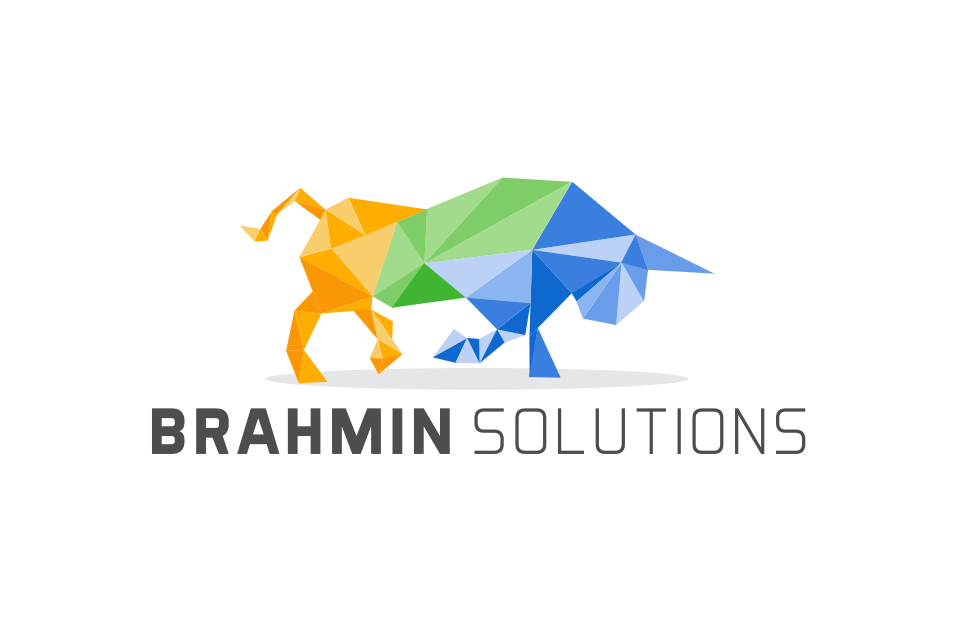
Manufacturing and Inventory Management Software
One of the biggest challenges for manufacturers is stock management. This means you must track what people are buying and whether you have enough of that product. It would be best to consider what new products people might want and how many of each product you should have.
Some manufacturers guess their safety stock, which can cause problems because they might not have enough of a product, and customers are upset, often leading to lost sales. A safety stock calculation can help you make decisions based on data which will help you keep more products in stock and make more money.
Before we explain how to use a safety stock formula, it’s helpful to define the term safety stock: Extra inventory held by a retailer or manufacturer in case demand increases is called safety stock. This means that inventory is above the desired amount you would usually have on hand to meet day-to-day needs.
One main reason manufacturers implement a safety stock strategy is to prevent stockouts. Stockouts are usually caused by:
It can be challenging to plan for and maintain a target inventory level. However, this is where a safety stock formula comes in. Lets take a look at the safety stock formula and how it fits with the ordering process.
The safety stock formula is:
SS = (Max Lead Time × Max Sale) – (Average Lead time × Average Sale)
You can calculate how much safety stock you need by using a spreadsheet. First, set up your spreadsheet like the image below. In the cell (column G) where you want your safety stock figure calculated for each product (SKU), type the formula:
Safety Stock = D2 =(C2*E2)-(D2*F2)
Where:
An inventory management system such as Brahmin Solutions is typically used to manage stock within ideal levels once a safety stock figure is set for each product.
The safety stock formula works in conjunction with the reorder point formula. The reorder point is the level where you need to reorder more products. The safety stock formula ensures enough stock by adding a buffer based on the maximum number of sales made over the maximum number of days of lead time.
If you manufacture products, you need to factor the time taken for production into your min and max lead times. Here three things to consider to ensure that your lead time accounts for all the production time:
Safety stock's purpose is to ensure that you always have enough product supply to sell. This is so that when customers buy the product and it will be delivered on time and you have all the parts you need for manufacturing. If you don't have enough stock, it can negatively affect your business in a few ways.
Stockouts can be harmful to customer satisfaction. If a clothing manufacturer runs out of a specific color of a shoe, it might not have much effect. It could be very bad if a business sells products to other B2B businesses and runs out of stock.
Excellent customer satisfaction is essential, but it is not the only thing affecting a business's bottom line. After all, you can have the best marketing campaign in the world, but if your product is unavailable when the consumer wishes to buy it, their money will undoubtedly go to your competitors.
A business running out of a raw material during manufacturing can be very harmful because it stops production. If the production run stopped, this can raise labor costs relative to output. However, if the production run is split, something else can be made while you wait for the missing stock to arrive. This added inefficiency makes it more challenging to produce items.
While it is important to avoid running out of stock, it is also essential to understand the risks associated with having too much inventory.
Having a lot of inventory costs money. This is because you have to pay for the stock and need more warehouse space, staff, and other costs.
A company holding too much inventory can lead to significant losses. Foods, beverages, and medicines are a few examples of things that might spoil or devalue. A company must balance the risk of not having enough inventory against the risk of having too much stock that never sells.
The specific job responsibilities for someone who sets safety stock levels vary depending on the size and type of company. In small companies, the owner or general manager might be responsible for this. But in larger businesses, production managers, warehouse managers, or operation managers might set the safety stock levels.
Often Safety stock becomes a priority because one of two things typically happens:
Not every product needs a buffer of safety stock. You need to decide how much is suitable for your company. The easy answer is that you need a safety stock level for any product or component you can't afford to run out of.
Brahmin Solutions allows you to manage safety stock in one of two ways:
To set your minimum stock level for each product, or SKU, you need to calculate the reorder point for each item. This is a level of stock that is calculated by factoring in both the safety stock level and the average quantity used between ordering stock and it arriving in the warehouse.
Once the reorder points are set, you can use Brahmin Solutions Reorder report to easily manage stock levels and avoid stock outs.
Reorder points can be calculated by Brahmin Solutions after your enter some parameters such as safety stock in days and the number of days you want your stock to be replenished. As demand changes, your reorder points will be recalculated.
A very important point to consider when you are calculating safety stock is whether your business is growing. If a business is growing rapidly it may need more than what was historically calculated as their Safety Stock figure since those numbers only reflect historic data from before when they were at lower levels. If a company is marketing more, expanding across more channels, it will have to adjust its safety stock accordingly to support this growth.